Abstract
This paper presents an in-depth analytical investigation into the time-dependent flow of a Casson hybrid nanofluid over a radially stretching sheet. The study introduces the effects of magnetic fields and thermal radiation, along with velocity and thermal slip, to model real-world systems for enhancing heat transfer in critical industrial applications. The hybrid nanofluid consists of three nanoparticles—Copper and Graphene Oxide—suspended in Kerosene Oil, selected for their stable and superior thermal properties. The theory of Darcy-Forchheimer, along with the suction and injection effect, is applied to refine the flow behaviour and enhance heat transfer efficiency. The governing nonlinear equations are solved using the Homotopy Analysis Method to provide a robust framework for solution accuracy. The graphical and tabulated results demonstrated that hybrid nanofluid outperforms mono and Casson hybrid nanofluids. The result shows that, at a nanoparticle volume concentration of 0.03, the Casson hybrid nanofluid showed a remarkable 19.99% increase in heat transfer, compared to 14.80% for simple nanofluid. The magnetic parameter and thermal radiation parameter further amplify thermal conductivity. This research provided a critical insight into optimizing thermal management systems for advanced engineering applications, positioning hybrid nanofluid as highly effective solutions for next-generation cooling technologies.
Similar content being viewed by others
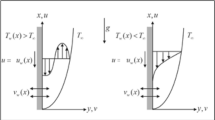
Introduction
The study of boundary layer flow and heat transfer over stretching sheet has garnered significant interest due to its vital role in industrial, engineering, and medical processes, such as glass fibre production, polymer extrusion, liquid metal handling, heat exchangers, cooling systems, drug delivery systems, and tissue engineering. Efficient heat transfer at the stretching surface is crucial for these applications. Crane1 laid the foundation by deriving an exact solution for incompressible viscous flow over a linearly stretching sheet, inspiring extensive research into various geometries and dynamic conditions. Akbar et al.2 extended this work to a three-dimensional magnetohydrodynamic non-Newtonian nanofluid, while Ullah et al.3 analyzed heat and mass transfer in slip flow over a permeable stretching surface. Siddique et al.4 explored the dynamics of a tangent hyperbolic nanofluid with concentration-dependent viscosity and motile microorganisms, and Ali et al.5 studied bioconvective slip flow to improve energy systems. Further studies by Nihaal et al.6 and Shivaraju et al.7 examined MHD Casson hybrid nanofluid flow under thermal radiation and a chemical reaction. Sekhar et al.8 analyzed viscoelastic nanofluid over a stretching sheet with slip condition, while Prakash et al.9 investigated hybrid nanofluid on an exponentially stretching surface under heat source effect. Axisymmetric flow over radially stretching a sheet has also been extensively studied, with Shah et al.10 focusing on two immiscible fluids under a magnetic field, Bhatti et al.11 investigating convection flow in a porous microchannel, and Umavathi et al.12 exploring radiative heat transfer in squeezing flow. Recent work has addressed time-dependent behaviour, including Azar et al.13 on porous wedge, Ali et al.14 on cross Casson hybrid nanofluid with entropy minimization, Abbas et al.15 on radiative Sutterby nanofluid, and Ullah et al.16 on MHD Casson hybrid nanofluid with nanoparticle shape. While mono and hybrid nanofluid have been extensively analyzed, the behaviour of Casson hybrid nanofluid in these geometries remains underexplored, motivating the present study.
Casson hybrid nanofluid (HNF), formed by dispersing two distinct nanoparticles in a base fluid, offered superior thermal and rheological properties compared to conventional nanofluid or base fluid alone. These properties make HNF highly suitable for applications in automotive radiators, microelectronics cooling, solar energy systems, and nuclear reactors. For instance, Madhukesh et al.17examined the thermal and flow behaviour of HNF over an extending surface, reporting enhanced heat transfer due to improved nanoparticle synergy. Similarly, Nihaal and Mahabaleshwar18 demonstrated significant thermal efficiency improvement with optimized volume fraction in HNF, highlighting their effectiveness in an advanced heat transfer system. Karthik et al.19 further investigated HNF embedded in porous media and observed enhanced thermal conductivity and efficient energy transport, making them ideal for a high-performance cooling system. In contrast, Casson HNF, composed of two types of nanoparticles, present even greater enhancements in thermal and rheological properties, making them ideal for advanced heat transfer applications like cooling automotive engines, solar collectors, and microelectronics. Studies on HNF, such as Cu + Al2O3 in water, have demonstrated superior thermal efficiency and momentum flow compared to both mono and Casson HNF. Additionally, Nasir et al.20 confirmed that HNF composition significantly enhanced thermal conductivity and energy transport, making HNFs an emerging focus for advanced cooling systems and high-efficiency thermal management applications.
This study analytically investigated the flow of Casson hybrid nanofluid over a radially stretching sheet, focusing on the effect of magnetic field, thermal radiation, and slip condition. Adnan et al.21 highlighted the role of magnetic field and radiation in enhancing heat transfer in hybrid nanofluid, while Khan et al.22 demonstrated that multiple slip conditions and thermal radiation significantly improve heat and mass transfer. The impact of suction and injection on flow characteristics is examined using the theory of Darcy-Forchheimer, building on the finding of Panda et al.23 and Kumari et al.24. Their results showed the optimization potential of a suction parameter. Additionally, Khan et al.25 and Sekhar et al.8 explored the effect of thermal radiation and a heat source on nanofluid flow, emphasizing their importance in thermal management. The homotopy analysis method (HAM) is employed to solve the governing equations, following the approach of Sohail et al.26, who validated its effectiveness in analyzing unsteady dynamics over a stretching sheet. This study underscores the potential of hybrid nanofluids in enhancing thermal efficiency for industrial applications.
This study advances the understanding of Casson hybrid nanofluid behaviour by exploring its time-dependent flow dynamics over a radially stretching sheet, particularly under the influence of magnetic fields, thermal radiation, and slip conditions. While related work exists in the literature, this research fills a critical gap by extending the Darcy-Forchheimer theory to include suction and injection effects, thereby providing a more comprehensive analysis of flow behaviour and heat transfer efficiency. The novelty lies in demonstrating the superior thermal performance of Casson hybrid nanofluids with copper and graphene oxide nanoparticles in kerosene oil, achieving a remarkable 19.99% increase in heat transfer at a nanoparticle concentration of 0.03. This work raises key questions, such as: How do magnetic and thermal radiation parameters amplify thermal conductivity? What specific roles do suction and injection play in optimizing the thermal management of advanced cooling technologies? These insights aim to guide future research and industrial applications in next-generation heat transfer systems.
Mathematical formulation
Consider an unsteady two-dimensional and laminar flow of Casson hybrid nanofluid over a stretching surface as shown in Fig. 1. The configuration consists of a sheet positioned at z = 0, which occupies the space z > 0. A cylindrical polar coordinate system (r, θ, z) was utilized for computational analysis. T (r, z, t) represents the temperature, indicating its dependence on radial position (r), axial position (z), and time (t). The velocity field [v (r, z, t)] is a vector containing radial (u) and axial (w) components. The fluid’s temperature takes the form \({T_w}={T_\infty }+{\raise0.7ex\hbox{${br}$} \!\mathord{\left/ {\vphantom {{br} {1 - at}}}\right.\kern-0pt}\!\lower0.7ex\hbox{${1 - at}$}}\). Here Tw denotes the wall temperature, while ∞denotes the far-field temperature3,27,28,29.
As we expand \({q_r}\) using the Taylor series and disregarding higher-order terms, it can be expressed in the following manner.
By incorporating this term into the energy equation, we derive the following outcome.
The boundary conditions near and distant from the sheet are:
\(u={U_w}+{U_{slip}},w={W_0}= - 2\Lambda \sqrt {\frac{{{U_w}{\upsilon _f}}}{r}} ,T={T_w}+{T_{slip}}\) at \(z=0\)
\(u \to {u_\infty },T \to {T_\infty }\) as \(z \to \infty\)
The sheet undergoes radial expansion with a surface velocity \({U_w}={{\gamma r} \mathord{\left/ {\vphantom {{\gamma r} {1 - at}}} \right. \kern-0pt} {1 - at}}\), and stream velocity \({u_\infty }\), the variables γ and a indicate parameters that describe the physical properties of the stretching surface. The term \({U_{slip}}={N_1}\frac{{\partial u}}{{\partial z}}\) and \({T_{slip}}={N_2}\frac{{\partial T}}{{\partial z}}\) is represented the slip velocity and slip temperature respectively with the hydraulic slip \({N_1}\) and thermal slip \({N_2}\) factors. Here the surface \({W_0}>0\left( {\Lambda <0} \right)\) represents injection and \({W_0}<0\left( {\Lambda>0} \right)\) represents suction. A magnetic field with a strength of \({B_0}\left( t \right)={{{B_0}} \mathord{\left/ {\vphantom {{{B_0}} {\sqrt {1 - at} }}} \right. \kern-0pt} {\sqrt {1 - at} }}\) acts perpendicular to the stretching sheet. This model considers the impacts of suction, joule heating, and viscous dissipation. Also adopting the Darcy–Forchheimer concept to the flow model, the permeability of the porous medium is represented by k0, and \({{{F_0}={C_b}} \mathord{\left/ {\vphantom {{{F_0}={C_b}} {r\sqrt {{k_o}} }}} \right. \kern-0pt} {r\sqrt {{k_o}} }}\) is the Forchheimer number, where Cb is the drag coefficient. The experimental values of the nanoparticles and base fluid are presented in Table 1. The thermophysical properties of the ternary nanofluid model are described in Table 2 as can be seen.
The method of similarity transformation applied in this study is demonstrated as follows
\(\psi =\frac{{ - {r^2}{U_w}}}{{\sqrt {\operatorname{Re} } }}f\left( \eta \right)\), \(\eta =\frac{z}{r}\sqrt {\operatorname{Re} }\) and \(T=\Theta \left( \eta \right)\left( {{T_w} - {T_\infty }} \right)+{T_\infty }\)
The stream function () now represents the velocity components in both the longitudinal and transverse directions.
\(u=\frac{1}{r}\frac{{\partial \psi }}{{\partial z}}{\text{ }},w=\frac{1}{r}\frac{{\partial \psi }}{{\partial r}}.\)
This satisfies the continuity equation.
Similarity transformations are applied to convert the momentum and energy equations into a nondimensional form.
\(\frac{{{\upsilon _{hnf}}}}{{{\upsilon _f}}}\left( {\left( {1+\frac{1}{\beta }} \right)f^{\prime\prime\prime} - \frac{1}{{\lambda \cdot \operatorname{Re} }}f^{\prime}} \right)+2f\cdot f^{\prime\prime} - \left( {1+Fr} \right){f^{\prime {2}}} - S\left( {f^{\prime}+\frac{\eta }{2}f^{\prime\prime}} \right) - \frac{{{{{\sigma _{hnf}}} \mathord{\left/ {\vphantom {{{\sigma _{hnf}}} {{\sigma _f}}}} \right. \kern-0pt} {{\sigma _f}}}}}{{{{{\rho _{hnf}}} \mathord{\left/ {\vphantom {{{\rho _{hnf}}} {{\rho _f}}}} \right. \kern-0pt} {{\rho _f}}}}}{M_g}f^{\prime}=0\)
\(\frac{1}{{{\operatorname{P} _r}}}\left( {\frac{{{k_{hnf}}}}{{{k_f}}}+\frac{4}{3}Rd} \right)\Theta ^{\prime\prime}+\frac{{{{\left( {\rho {c_p}} \right)}_{hnf}}}}{{{{\left( {\rho {c_p}} \right)}_f}}}\left( \begin{gathered} {\text{ }}2f\Theta ^{\prime} \hfill \\ - \frac{\eta }{2}S\Theta ^{\prime} \hfill \\ \end{gathered} \right)+\frac{{{\mu _{hnf}}}}{{{\mu _f}}}{E_c}{f^{\prime\prime{2}}}+\frac{{{{{\sigma _{hnf}}} \mathord{\left/ {\vphantom {{{\sigma _{hnf}}} {{\sigma _f}}}} \right. \kern-0pt} {{\sigma _f}}}}}{{{{{{\left( {\rho {c_p}} \right)}_{hnf}}} \mathord{\left/ {\vphantom {{{{\left( {\rho {c_p}} \right)}_{hnf}}} {{{\left( {\rho {c_p}} \right)}_f}}}} \right. \kern-0pt} {{{\left( {\rho {c_p}} \right)}_f}}}}}{M_g}{E_c}{f^{\prime\prime{2}}}=0\)
The boundary condition (4) now transforms into.
\(f^{\prime}=1+{l_1}f^{\prime\prime},{\text{ }}f={S_p},{\text{ }}\Theta =1+{l_2}\Theta ^{\prime}\) at \(\eta =0\) and \(f^{\prime} \to 0,{\text{ }}\Theta \to 0\) as \(\eta \to \infty\)
Dimensionless parameters
\(\begin{gathered} S=\frac{a}{\gamma },{\text{ }}M=\frac{{{\sigma _f}B_{0}^{2}}}{{\gamma {\rho _f}}},{\text{ }}Fr=\frac{{{c_b}}}{{\sqrt {{k_0}} }},{\text{ }}\lambda =\frac{{{k_0}}}{{{r^2}}},{\text{ }}\operatorname{Re} =\frac{{r{U_w}}}{{{\upsilon _f}}},{\text{ }}Ec=\frac{{U_{w}^{2}}}{{\left( {{T_w} - {T_\infty }} \right){c_p}}},{\text{ }}Rd=\frac{{4{\delta ^*}{T^3}}}{{3{k_f}{k^*}}}, \hfill \\ {\text{ }}\Pr =\frac{{{\alpha _f}}}{{{\upsilon _f}}},{l_1}={N_1}\sqrt {\frac{{{U_w}}}{{r{\upsilon _f}}}} ,{\text{ }}{l_2}={N_2}\sqrt {\frac{{{U_w}}}{{r{\upsilon _f}}}} . \hfill \\ \end{gathered}\)
Physical quantities
Local shear rate (Cf) and Nusselt number (Nu) are the key physical factors that determine the flow challenge, denoted as \({C_f}={\raise0.7ex\hbox{${{\tau _w}}$} \!\mathord{\left/ {\vphantom {{{\tau _w}} {{\rho _f}U_{w}^{2}}}}\right.\kern-0pt}\!\lower0.7ex\hbox{${{\rho _f}U_{w}^{2}}$}}\;\) & \(Nu={\raise0.7ex\hbox{${r{q_w}}$} \!\mathord{\left/ {\vphantom {{r{q_w}} {{k_f}\left( {{T_w} - {T_\infty }} \right)}}}\right.\kern-0pt}\!\lower0.7ex\hbox{${{k_f}\left( {{T_w} - {T_\infty }} \right)}$}}\), respectively, where \({\tau _w}={\mu _{hnf}}\frac{{\partial u}}{{\partial z}}\) & \({q_w}= - \left( {{k_{hnh}}+\frac{3}{4}Rd} \right)\frac{{\partial T}}{{\partial z}}\) at \(z=0\). The values of the shear rate coefficient and heat flow at \(z=\infty\) can be simplified in non-dimensional form as \({C_f}\sqrt {\operatorname{Re} } ={\raise0.7ex\hbox{${{\mu _{hnf}}}$} \!\mathord{\left/ {\vphantom {{{\mu _{hnf}}} {{\mu _f}}}}\right.\kern-0pt}\!\lower0.7ex\hbox{${{\mu _f}}$}}f^{\prime\prime}\left( 0 \right)\) & \(Nu{\operatorname{Re} ^{ - {1 \mathord{\left/ {\vphantom {1 2}} \right. \kern-0pt} 2}}}=\left( {\frac{{{k_{hnf}}}}{{{k_f}}}+\frac{3}{4}Rd} \right)\Theta ^{\prime}\left( 0 \right)\) .
Solution methodology
Introducing the method for solving considered nonlinear problems called the homotopy analysis method (HAM), created by Professor Shijun Liao33. This technique uses the topological idea of homotopy to produce a convergent series solution for nonlinear systems. The system of ordinary differential equations that the series solutions come from was created using the HAM approach. Linear operators \({L_1}\& {L_2}\) and initial guesses \({f_0}\left( \eta \right)\& {\Theta _0}\left( \eta \right)\) are taken in the form given following:
\({L_1}=f^{\prime\prime\prime}+f^{\prime\prime},{\text{ }}{L_2}=\Theta ^{\prime\prime}+\Theta ^{\prime}\)
\({f_0}\left( \eta \right)=\frac{{1 - {{\text{e}}^{ - x}}+{S_p}+{l_1}{S_p}}}{{1+{l_1}}},{\text{ }}\& {\text{ }}{\Theta _0}\left( 0 \right)=\frac{{{{\text{e}}^{ - x}}}}{{1+{l_2}}}.\)
Subject to the following properties
In which \({D_i}\left( {i=1 - 5} \right)\) is the constant. The problems have been constructed for zeroth and mth order distortion as given the above linear operators. The problems have been resolved with the help of Mathematica software.
Results validation/ HAM convergence
To verify our results, the convergence ___domain and the pace of homotopic solutions of ternary hybrid nanofluid flow are regulated by the non-zero convergence control parameters (CCPs) \({h_f}\)and \({h_\Theta }\). We have used Liao’s definition of depreciation by average mean square errors31 to get the ideal value of CCPs.
Following Liao:
Where \(\varepsilon _{m}^{t}\)stands for total squared residual error, \(\delta \zeta =0.5\) and \(m=10\)the optimal values of CCPs at 2nd order of approximations for the hybrid nanofluid case are \({h_f}\varepsilon \left[ { - 2,0.5} \right]\) and \({h_\Theta }\varepsilon \left[ { - 1.7,0.4} \right]\) as shown in Fig. 2(a). The total squared residual error for the HAM solution is shown in Fig. 2(b), while Individual mean squared residual errors. Also, for better accuracy, Table 3 represents the comparative analysis of \(f^{\prime\prime}\left( 0 \right)\) against M with the existence literature [34, 35, 36].
Graphical and tabulated results and discussions
In this section, we presented and discussed the graphical results derived from the power series solution of the governing ordinary differential equations (ODEs) subject to the prescribed boundary conditions, using the Homotopy Analysis Method (HAM). The iterative power series solutions obtained through HAM are utilized to explore the effects of various dimensionless parameters on the fluid flow and heat transfer profiles.
The effect of velocity and thermal slip can be seen in Fig. 3(a-b) against velocity and temperature profiles. The velocity slip parameter (l1 = 0.2, 0.3, 0.4) decreases the velocity profile as the slip increases, reducing the interaction between the fluid and the surface. No further effect is observed when l1 = 0. The nanofluid (Cu + kerosene oil) has the highest velocity due to copper’s high thermal conductivity (765 W/m·K). The Casson hybrid nanofluid (Cu + GO + kerosene oil) shows the lowest velocity due to the higher density and specific heat capacity of graphene oxide (GO: 5000 W/m·K, 1800 kg/m³, 717 J/kg·K), causing greater inertia. Conversely, for temperature profiles, the thermal slip parameter decreases the temperature as it limits heat transfer, with the Casson hybrid nanofluid showing the highest temperature due to GO’s superior heat retention, followed by the Casson hybrid nanofluid and the nanofluid, which has the lowest temperature owing to copper’s lower specific heat capacity (531.8 J/kg·K).
Figure 4(a-b) shows the Forchheimer parameter influences the behaviour of nanofluids, Casson hybrid nanofluids, and Casson hybrid nanofluids, particularly regarding velocity and temperature profiles under both slip and no-slip conditions. For the Cu + Kerosene Oil nanofluid, the high thermal conductivity of copper (765 W/m·K) facilitates effective heat transfer, yet the low thermal conductivity of kerosene oil (0.145 W/m·K) may lead to substantial temperature gradients, especially under no-slip conditions. As the Forchheimer parameter (Fr) increases, inertial effects become more pronounced, resulting in flatter velocity profiles and reduced velocity gradients. The Cu + GO + Kerosene Oil Casson hybrid nanofluid, leveraging the exceptionally high thermal conductivity of graphene oxide (5000 W/m·K), exhibits improved heat distribution and reduced temperature gradients, particularly under slip conditions, where the fluid can move more freely along the boundaries. Overall, as the Forchheimer parameter increases, both slip and no-slip conditions enhance the fluid’s thermal efficiency, with higher thermal conductivity materials leading to better heat transfer and smoother velocity profiles in applications involving fluid flow in porous media.
The presence of a magnetic field influences the velocity and temperature profiles of nanofluids, with notable differences across various compositions as shown in Fig. 5(a-b). As the magnetic parameter increases, the velocity profile generally decreases due to the resistance posed by Lorentz forces, leading to flatter velocity distributions, especially under no-slip conditions. Conversely, this magnetic field enhances thermal mixing, resulting in increased temperature profiles across the fluid. The Casson hybrid nanofluid (Cu + GO + Kerosene Oil) demonstrates the best temperature performance due to the high thermal conductivity of graphene oxide (5000 W/m·K), which facilitates effective heat transfer and uniform temperature distributions. In contrast, the Cu + Kerosene Oil nanofluid exhibits superior velocity performance, as the high conductivity of copper (765 W/m·K) allows it to maintain better flow characteristics despite the magnetic influence. Thus, while the magnetic field dampens the velocity profiles across all nanofluids, it paradoxically enhances the temperature profiles, showcasing the Casson hybrid nanofluid’s effectiveness in temperature uniformity and the copper-based nanofluid’s advantage in velocity performance.
The unsteady parameter negatively impacts both the velocity and temperature profiles of nanofluids under slip and no-slip conditions. This scenario is captured in Fig. 6(a-b) as can be seen. The time-dependent effects the evident as the unsteady parameter increases, which brings a decrease in the velocity profile due to increased inertia and viscous damping forces. This force hinders fluid motion This reduction is evident in both slip and no-slip conditions. The temperature profile also decreases, as the unsteady effects disrupt the thermal equilibrium and mixing within the fluid. While the unsteady parameter decreases both velocity and temperature profiles, the Casson hybrid nanofluid excels in maintaining temperature uniformity, whereas the copper-based nanofluid demonstrates superior velocity performance under these dynamic conditions.
As shown in Fig. 7(a-b), the suction/injection parameter affects the velocity and temperature profiles in both slip and no-slip scenarios. Applying suction improves the velocity profile by pushing the fluid in the direction of the boundary. With a density of 632 kg/m³ for copper and 783 kg/m³ for kerosene oil, the Cu + Kerosene Oil nanofluid benefits most from this effect, allowing the fluid to sustain a greater velocity. A more uniform but lower velocity profile can result from the injection’s tendency to lower the velocity profile, which can also damper the current flow. Suction and injection have an important influence on temperature profiles as well. Suction enhances the temperature profile by promoting better mixing and reducing thermal gradients, particularly in the Casson hybrid nanofluid (Cu + GO + Kerosene Oil), due to the superior thermal conductivity of graphene oxide (5000 W/m·K) and the densities of its components—copper (632 kg/m³), silver (10,500 kg/m³), and kerosene oil (783 kg/m³).
The Eckert number and thermal radiation parameter significantly influence the velocity profiles of nanofluids under both slip and no-slip conditions are drawn in Fig. 8(a-b). As the Eckert number increases, the impact of viscous dissipation becomes more pronounced, particularly in no-slip conditions, leading to reduced velocities as kinetic energy contributes to heating rather than enhancing motion; for instance, in the Cu + Kerosene Oil nanofluid, the high thermal conductivity of copper (765 W/m·K) results in flatter velocity profiles. In slip conditions, while the effect of the Eckert number is mitigated, velocities may still decrease slightly due to viscous effects. Conversely, an increase in the thermal radiation parameter enhances heat transfer, promoting more uniform temperature distributions that can reduce viscosity and increase velocity profiles; this is especially evident in the Casson hybrid nanofluid (Cu + GO + Kerosene Oil), where graphene oxide’s exceptional conductivity (5000 W/m·K) significantly boosts fluid velocities. Overall, the interplay between the Eckert number and thermal radiation parameter determines the flow dynamics, with the Casson hybrid nanofluid demonstrating superior velocity performance due to enhanced heat transfer characteristics.
The magnetic parameter increases skin friction and decreases the Nusselt number, but the effects differ in intensity due to slip and no-slip conditions as shown in Fig. 9(a-b). In slip conditions, the magnetic parameter increases skin friction by creating resistance (Lorentz forces), which is the cause of increasing friction. Additionally, the Nusselt number is lowered by the magnetic parameter, limiting convective heat transport. Because there is no slide at the boundary, there is less of an increase in skin friction, and improved convective heat transmission results in a less noticeable fall in the Nusselt number. The Casson hybrid nanofluid (Cu + GO + Kerosene Oil) performs best in maintaining heat transfer under these conditions, thanks to the high thermal conductivity of graphene oxide (5000 W/m·K), while Cu + Kerosene Oil exhibits better flow performance, reducing the impact on skin friction.
Heat enhancement is calculated percentage-wise for the Casson hybrid nanofluid, Casson hybrid nanofluid and simple nanofluid versus nanoparticles volume concentration in Table 4 as can be seen. Using the following formula:
\(\frac{{Kerosene{\text{ }}Oil{\text{ without nanoparticles}}}}{{Kerosene{\text{ }}Oil{\text{ }}with{\text{ nanoparticles}}}} \times 100={\text{Obtained Results,}}\)
\({\text{Obtained Results}} - {\text{100}}={\text{Enhancement Percentage}}{\text{.}}\)
Also, with the help of these calculations, it is determined that the Casson hybrid nanofluid has the best ability to transfer heat compared to other fluids for the recently considered model.
Conclusion
The analysis of Casson hybrid nanofluid (HNF) flow over a radially stretching sheet has significant applications in various fields, including industrial cooling, thermal management, and advanced engineering systems. Understanding the dynamic behaviour of HNF under time-dependent conditions is essential for optimizing heat transfer processes and enhancing the performance of cutting-edge technologies. In this study, we analytically investigated the time-dependent flow of Casson HNF, incorporating Copper and Graphene Oxide nanoparticles dispersed in Kerosene Oil. The impacts of magnetic fields, thermal radiation, suction and injection effects, and velocity and thermal slip conditions were comprehensively examined. The governing equations were transformed into nonlinear dimensionless differential equations and solved using the Homotopy Analysis Method (HAM). The core of study innovation also includes the extension of Darcy-Forchheimer theory along with the suction and injection effect and the demonstration of a 19.99% improvement in heat transfer performance, positioning Casson HNF as a promising solution for next-generation thermal management systems. The conclusion points provide a comprehensive summary of the recent research findings and their implications, demonstrating the significance of work in the field.
-
The Casson hybrid nanofluid (Cu + GO + Kerosene Oil) exhibits superior temperature profiles due to the exceptional thermal conductivity of graphene oxide (5000 W/m·K), facilitating effective heat transfer and promoting uniform temperature distributions under various flow conditions.
-
The Cu + Kerosene Oil nanofluid demonstrates the best velocity performance, primarily due to the high thermal conductivity of copper (765 W/m·K) and its favourable density (632 kg/m³), which allows for better flow characteristics, especially under slip conditions.
-
Increasing the magnetic parameter dampens velocity profiles across all nanofluids due to the opposing Lorentz forces, leading to flattened velocity distributions, while simultaneously enhancing temperature profiles through improved thermal mixing, particularly in Casson hybrid and Casson hybrid nanofluids.
-
The unsteady parameter adversely affects both velocity and temperature profiles, with higher values leading to decreased velocities and increased thermal gradients; however, the Casson hybrid nanofluid maintains better thermal performance due to its high thermal conductivity components.
-
Suction significantly enhances velocity profiles by increasing fluid momentum, particularly in the Cu + Kerosene Oil nanofluid, while the Casson hybrid nanofluid excels in temperature uniformity due to effective mixing under suction conditions. Conversely, injection tends to reduce both velocity and temperature profiles.
-
The Eckert number negatively impacts velocity profiles due to increased viscous dissipation, especially in no-slip conditions, whereas the thermal radiation parameter enhances heat transfer, resulting in improved velocities in both slip and no-slip scenarios, particularly for the Casson hybrid nanofluid.
-
The results indicate that the Casson hybrid nanofluid (Cu + GO + Kerosene Oil) consistently demonstrates superior heat transfer performance, with up to a 6.55% enhancement in Nusselt number compared to the base nanofluid (Cu + Kerosene Oil) at a nanoparticle volume concentration of 0.01. Additionally, the Casson hybrid nanofluid (Cu + Kerosene Oil) shows a moderate improvement, with a maximum heat transfer enhancement of 4.06% at the same concentration.
-
The Homotopy Analysis Method (HAM) employed in this study demonstrates high accuracy in predicting the velocity and temperature profiles of the nanofluids. Its flexibility in handling nonlinear differential equations allows for precise modelling of complex fluid behaviours under varying conditions, reinforcing the reliability of the results obtained.
-
The findings underscore the potential of using nanofluids, particularly those incorporating graphene oxide, for applications requiring efficient heat transfer and flow dynamics, such as in cooling systems, thermal energy storage, and various industrial processes.
-
Further investigations into the effects of varying concentrations of nanoparticles, different base fluids, and additional flow conditions are recommended to optimize the performance of nanofluids in real-world applications.
Data availability
The datasets used and/or analysed during the current study available from the corresponding author on reasonable request.
Abbreviations
- \({B_0}\) :
-
Magnetic field (NA-1m-1)
- u:
-
Velocity Components (ms-1)
- F (η):
-
Dimensionless velocities
- F0 :
-
Non-uniform inertia coefficient
- \(T_\infty\) :
-
Ambient temperature (K)
- M:
-
Magnetic parameter
- r, z & φ:
-
Cylindrical coordinates (m)
- T:
-
Fluid temperature (K)
- Tw :
-
surface temperature
- qr :
-
Radiation heat flux (kgs-3)
- k:
-
Thermal conductivity (wm-1K-1)
- \({k_0}\) :
-
Permeability of porous space
- \(\Theta (\mu)\) :
-
Dimensionless temperature
- Re:
-
Reynold number
- Pr:
-
Prandtl number
- Ec:
-
Eckert number
- \(C_f\) :
-
Skin friction
- Nu:
-
Nusselt number
- \(\mu\) :
-
Dynamic viscosity (kgm-1s-1)
- λ:
-
Porosity Parameter
- υ:
-
Kinematic viscosity (m2s-1)
- ρ:
-
Density (kgs-3)
- \(\phi\) :
-
Volume fraction nanoparticles
- \(\rho c_p\) :
-
Specific heat capacity (jkg-1K-1)
- θ:
-
Angle
- f:
-
Base Fluid
- nf:
-
Nanofluid
- hnf:
-
Ternary hybrid nanofluid
- ∞:
-
Ambient condition
References
Crane, L. J. Flow past a stretching plate. Z. für Angewandte Math. und Physik ZAMP. 21, 645–647 (1970).
Akbar, N. S., Al-Zubaidi, A., Saleem, S. & Alsallami, S. A. Variable fluid properties analysis for thermally laminated 3-dimensional magnetohydrodynamic non-newtonian nanofluid over a stretching sheet. Sci. Rep. 13 (1), 3231 (2023).
Ullah, H. et al. A numerical study of heat and mass transfer characteristic of three-dimensional thermally radiated bi-directional slip flow over a permeable stretching surface. Sci. Rep. 14 (1), 19842 (2024).
Siddique, I. et al. Significance of concentration-dependent viscosity on the dynamics of tangent hyperbolic nanofluid subject to motile microorganisms over a non-linear stretching surface. Sci. Rep. 12 (1), 12765 (2022).
Ali, F. et al. Bioconvective applications of unsteady slip flow over a tangent hyperbolic nanoliquid with surface heating: improving energy system performance. Int. J. Appl. Comput. Math. 8 (6), 276 (2022).
Nihaal, K. M., Mahabaleshwar, U. S. & Joo, S. W. Darcy Forchhiemer imposed exponential heat source-sink and activation energy with the effects of bioconvection over radially stretching disc. Sci. Rep. 14 (1), 7910 (2024).
Shivaraju, N. et al. Role of chemical processes and porous media in thermal transport of Casson nanofluid flow: a study with Riga plates. Case Stud. Therm. Eng. 64, 105395 (2024).
Sekhar, P. R., Sreedhar, S., Ibrahim, S. M., Kumar, P. V. & Omprakash, B. Numerical investigation of heat radiation on MHD viscoelastic nanofluid flow over a stretching sheet with heat source and slip conditions. Int. J. Interact. Des. Manuf. (IJIDeM). 18 (5), 2991–3000 (2024).
Prakash, O., Rao, P. S., Sharma, R. P. & Mishra, S. R. Casson hybrid nanofluid MHD motion towards an exponentially stretching/shrinking sheet with the effect of thermal radiation, heat source and viscous dissipation. Pramana 97 (2), 64 (2023).
Shah, N. A., Alrabaiah, H., Vieru, D. & Yook, S. J. Induced magnetic field and viscous dissipation on flows of two immiscible fluids in a rectangular channel. Sci. Rep. 12 (1), 39 (2022).
Bhatti, M. M., Bég, O. A., Ellahi, R. & Abbas, T. Natural convection non-newtonian EMHD dissipative flow through a microchannel containing a non-darcy porous medium: Homotopy perturbation method study. Qualitative Theory Dyn. Syst. 21 (4), 97 (2022).
Umavathi, J. C., Vajravelu, K., Bég, O. A. & Khan, U. F. Unsteady squeezing flow of a magnetized dissipative non-newtonian nanofluid with radiative heat transfer and fourier-type boundary conditions: numerical study. Arch. Appl. Mech. 92 (9), 2695–2711 (2022).
Azar, A. A., Jalili, P., Moziraji, Z. P., Jalili, B. & Ganji, D. D. Analytical solution for MHD nanofluid flow over a porous wedge with melting heat transfer. Heliyon ;10(15). (2024).
Ali, F. et al. Radiative flow of cross Casson hybrid Casson hybrid nanofluid (MoS2, TiO2, Ag/CMC-water) in a Darcy Forchheimer porous medium over a stretching cylinder with entropy minimization. Heliyon ;10(14). (2024).
Abbas, N., Shatanawi, W., Hasan, F. & Mustafa, Z. Thermal analysis of radiative Sutterby nanofluid flow over stretching curved surface. Heliyon ;10(13). (2024).
Ullah, B., Khan, U., Wahab, H. A., Khan, I. & Alam, M. N. Entropy generation analysis for MHD flow of Casson hybrid nanofluids over a curved stretching surface with shape effects. J. Nanomaterials. 2022 (1), 8929985 (2022).
Madhukesh, J. K. et al. Implementation of stacking regressor model on the flow induced by TiO2‐H2O and Ti6Al4V‐H2O nanofluid with waste discharge concentration. ZAMM-Journal Appl. Math. Mechanics/Zeitschrift für Angewandte Math. und Mechanik. 104 (12), e202300796 (2024).
Nihaal, K. M. & Mahabaleshwar, U. S. Heat and mass transfer analysis of hybrid nanofluid flow over a rotating permeable cylinder: a modified Buongiorno model approach. Hybrid. Adv. 6, 100243 (2024).
Karthik, K. et al. Computational analysis of water-based silver, copper, and alumina hybrid nanoparticles over a stretchable sheet embedded in a porous medium with thermophoretic particle deposition effects. Nanatechnol. Reviews. 13 (1), 20240083 (2024).
Nasir, S. et al. Heat transport study of Casson hybrid Casson hybrid nanofluid flow under magnetic dipole together with nonlinear thermal radiation. Appl. Nanosci. 12 (9), 2777–2788 (2022).
Adnan, Abbas, W., Said, N. M., Mishra, N. K., Mahmood, Z. & Bilal, M. Significance of coupled effects of resistive heating and perpendicular magnetic field on heat transfer process of mixed convective flow of Casson hybrid nanofluid. J. Therm. Anal. Calorim. 149 (2), 879–892 (2024).
Khan, Z. H., Khan, W. A., Ibrahim, S. M., Swain, K. & Huang, Z. Impact of multiple slips and thermal radiation on heat and mass transfer in MHD Maxwell hybrid nanofluid flow over porous stretching sheet. Case Stud. Therm. Eng. 61, 104906 (2024).
Panda, S., Ontela, S., Mishra, S. R. & Thumma, T. Effect of Arrhenius activation energy on two-phase nanofluid flow and heat transport inside a circular segment with convective boundary conditions: optimization and sensitivity analysis. Int. J. Mod. Phys. B. 38 (25), 2450342 (2024).
Kumari, A., Kumar, A. & Tripathi, R. Insight into the thermocapillary radiative flow of hybrid nanoliquid film over an infinite rotating disk with entropy generation and heat source. Int. J. Mod. Phys. B. 38 (21), 2450279 (2024).
Khan, Z. H., Swain, K., Ibrahim, S. M., Khan, W. A. & Huang, Z. Transient flow and heat transfer characteristics of single-phase nanofluid past a stretching sheet under the influence of thermal radiation and heat source. Alexandria Eng. J. 108, 122–134 (2024).
Sohail, M., Rafique, E., Singh, A. & Tulu, A. Engagement of modified heat and mass fluxes on thermally radiated boundary layer flow past over a stretched sheet via OHAM analysis. Discover Appl. Sci. 6 (5), 240 (2024).
Usman, M., Gul, T., Khan, A., Alsubie, A. & Ullah, M. Z. Electromagnetic couple stress film flow of hybrid nanofluid over an unsteady rotating disc. Int. Commun. Heat Mass Transfer. 127, 105562 (2021).
Tripathi, R. & Kumari, A. Capturing the onset of thermocapillary convection in the Cattaneo–Christov flow of electrically conducting thin film of Welan gum solution. Waves in Random and Complex Media. Mar 22:1–9. (2022).
Alkaoud, A., Khader, M. M., Eid, A. & Megahed, A. M. Numerical simulation of the flow of a tangent hyperbolic fluid over a stretching sheet within a porous medium, accounting for slip conditions. Heliyon ;10(8). (2024).
Agarwal, D. K., Vaidyanathan, A. & Kumar, S. S. Experimental investigation on thermal performance of kerosene–graphene nanofluid. Exp. Thermal Fluid Sci. 71, 126–137 (2016).
Bilal, M. et al. Novel numerical and artificial neural computing with experimental validation towards unsteady micropolar nanofluid flow across a Riga plate. Sci. Rep. ; 15(759). (2025).
Kumar, A., Sethy, P., Ray, A. K. & Kumari, A. Mixed convection magnetohydrodynamic flow of hybrid nanofluid over a spinning sphere with nonlinear thermal radiation: Keller-Box approach. Numerical Heat transfer, part A: applications. Nov 20, 1–27 (2023).
Liao, S. Homotopy analysis method: a new analytical technique for nonlinear problems. Commun. Nonlinear Sci. Numer. Simul. 2 (2), 95–100 (1997).
Turkyilmazoglu, M. MHD fluid flow and heat transfer due to a stretching rotating disk. Int. J. Therm. Sci. 51, 195–201 (2012).
Kumar, A., Tripathi, R., Singh, R. & Seth, G. S. Three-dimensional magnetohydrodynamic flow of micropolar CNT-based nanofluid through a horizontal rotating channel: OHAM analysis. Indian J. Phys. 94, 319–332 (2020).
Hayat, T., Bashir, G., Waqas, M. & Alsaedi, A. MHD flow of Jeffrey liquid due to a nonlinear radially stretched sheet in presence of newtonian heating. Results Phys. 6, 817–823 (2016).
Acknowledgements
N/A.
Author information
Authors and Affiliations
Contributions
Amal F. Alharbi: Conceptualization, Methodology, Investigation, Writing – original draft. Fida Mohammad: Review writing, Conceptualization, Methodology. Muhammad Usman: Visualization, Supervision, Visualization. Naseem Khan: Formal analysis, Conceptualization. Walid Abushiba: Review writing, Data curation. All authors have read and agreed to the published version of the manuscript.
Corresponding author
Ethics declarations
Competing interests
The authors declare no competing interests.
Additional information
Publisher’s note
Springer Nature remains neutral with regard to jurisdictional claims in published maps and institutional affiliations.
Rights and permissions
Open Access This article is licensed under a Creative Commons Attribution 4.0 International License, which permits use, sharing, adaptation, distribution and reproduction in any medium or format, as long as you give appropriate credit to the original author(s) and the source, provide a link to the Creative Commons licence, and indicate if changes were made. The images or other third party material in this article are included in the article’s Creative Commons licence, unless indicated otherwise in a credit line to the material. If material is not included in the article’s Creative Commons licence and your intended use is not permitted by statutory regulation or exceeds the permitted use, you will need to obtain permission directly from the copyright holder. To view a copy of this licence, visit http://creativecommons.org/licenses/by/4.0/.
About this article
Cite this article
Alharbi, A.F., Mohammad, F., Usman, M. et al. Thermophysical analysis of time-dependent magnetized Casson hybrid nanofluid flow (Cu + GO/Kerosene Oil) using Darcy-Forchheimer and thermal radiative models for industrial cooling applications. Sci Rep 15, 3398 (2025). https://doi.org/10.1038/s41598-025-87743-9
Received:
Accepted:
Published:
DOI: https://doi.org/10.1038/s41598-025-87743-9