Abstract
Boric acid and other impurities on the surface of boron (B) particles can interact with hydroxyl-terminated polybutadiene (HTPB), weakening the mechanical properties and energy release efficiency of boron-based solid rocket propellants. SA@B composite particles were created by coating stearic acid (SA) on the surface of B particles through solvent evaporation-induced self-assembly. The study investigated the impact of SA coating on the combustion performance of B particles and the mechanical properties of HTPB matrix composites. The results showed that the SA coating enhanced the oxidation efficiency of B particles in air. The combustion heat of SA@B composite particles is 30.29 MJ/g, about 50% higher than that of B particles. During the combustion of SA@B composite particles, fewer molten solid particles surround the flame, which enhances the stability of the combustion process of the B particles. Furthermore, the SA coating effectively enhanced the dispersion of B particles in HTPB. At a stretching speed of 100 mm/min, the tensile strength of the SA@B/HTPB composite materials is higher than that of the B/HTPB composite materials. Moreover, when the mass loading of the SA@B composite particles reaches 50 wt%, the tensile strength of SA@B/HTPB composite materials is 2.46 MPa. Activating the surface of boron particles with SA can significantly improve their compatibility with HTPB, which is crucial for the stable storage of boron-based solid rocket propellants.
Similar content being viewed by others
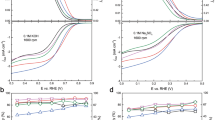
Introduction
Fuel-rich solid rocket propellant is a composite material that uses a polymer binder as its matrix and high-energy solid fuel as its filler. The theoretical calorific value of complete combustion of B particles is 58 MJ/kg, which has attracted much attention in fuel-rich solid rocket propellants1,2,3,4. The HTPB is commonly used as a polymer binder due to its low viscosity, resistance to aging, and exceptional low-temperature mechanical properties5,6,7. However, B particles are easily oxidized, and impurities such as boron trioxide (B2O3) and boric acid (H3BO3) are easily generated on their surfaces. These impurities can quickly react with HTPB, causing B to aggregate in the HTPB matrix. As a result, this affects the propellant’s preparation process and mechanical properties8,9,10. The accumulation of B particles in HTPB can lead to defects in the charge column and damage the overall structure, thus affecting the stable storage of boron-based solid rocket propellants. Moreover, when B particles react with oxygen to form a molten liquid oxide layer (B2O3, melting point: 460 °C, boiling point: 1860 °C) on their surface during combustion, the ignition of the B particles is significantly delayed, which, in turn, reduces the combustion efficiency of the B powder11,12,13.
Various methods have been reported to address the abovementioned issues, including mechanical ball milling, surface coating, ultrasonic mixing, combustible metal powder incorporation, and others14,15,16,17,18. These methods significantly enhance boron-based propellants’ high energy release efficiency and mechanical properties. By adding elements such as Mg, Al, transition metals (Co, Ni, Zr), metal oxides (Bi2O3, CuO, MgO), and other combustible metal powders, the B powders become easy to ignite and exhibit high energy release efficiency. This makes the B particles suitable for widespread use in solid propellants19. However, due to the non-uniformity of mechanical mixing, both heat and mass transfer are affected, which makes it challenging to enhance the ignition performance of B particles to a significant degree. One effective strategy to address the issues above is to construct a functional coating on the surface of B particles20,21,22. Numerous studies have demonstrated that employing fluorine-containing chemicals as surface coatings can effectively remove surface B particle oxides and augment the combustion reaction of B particles23,24. For example, using fluorographene as a coating material for B particles reduces the ignition delay time of B particles because of the good thermal conductivity of fluorographene and the erosion of the oxide layer of B particles25. Alternatively, fluoroalkyl silanes with three different lengths of fluorocarbon chains functionalize the surface of B particles, thereby enhancing their ignition characteristics and combustion performance26. The B particles were also coated with polyvinylidene fluoride (PVDF) through electrospinning. This process reduced the agglomeration size of the B particles and improved their combustion performance27. Although the literature has reported that fluorine-containing substances such as fluorographene, fluoroalkyl silane, and polyvinylidene fluoride significantly enhance the combustion performance of B particles, their environmental impacts are concerning. However, the poor compatibility between the B surface and HTPB leads to the accumulation of B particles in HTPB, which increases the curing time and weakens the mechanical properties of HTPB-based composites. Improving the compatibility between B and HTPB is the primary solution for enhancing the processing and mechanical properties of boron-based propellants. For instance, a chemical grafting technique was utilized to bond 2,4-toluene diisocyanate (TDI) and 3-amino-1,2,4-triazole (ATZ) to the surface of boron particles. The viscosity of the boron powder and HTPB system was measured using a rheometer to investigate the impact of various functionalized boron powders on HTPB compatibility28. Alternatively, B particles were coated with the ammonium perchlorate (AP) using the recrystallization method to study the effect of different AP contents on the rheological properties of the HTPB/B/AP composite slurry29. Although these studies on HTPB materials have substantially enhanced the compatibility between B and HTPB, the influence of these modified B particles on the macroscopic mechanical properties of B/HTPB composite materials remains unexplored. Consequently, research into the application of functionalized B particles in HTPB or other polymer composite materials and a deeper understanding of how functional coatings affect the mechanical properties of composite materials is necessary.
Stearic acid (SA) is a fatty acid widely found in nature and various oils and fats30. In recent years, SA has been widely used as a surface treatment to coat aluminum powders, enhancing its oxidation resistance, handling safety, and promoting a more controlled reactivity upon heating. For example, stearic acid-modified aluminum powder was prepared using SA as the surface protection layer for nanometer-sized aluminum powder. This modified nano-aluminum powder exhibits good moisture resistance, which ensures the thermal stability of nano-aluminum/nickel composite materials.31. To ensure the safety of SA-coated aluminum powder in practical applications, Zhang et al. studied the effect of SA coating on aluminum dust’s combustion and explosion performance. SA coating is conducive to inhibiting the explosion of aluminum dust, and they proposed a physical model of the explosion process of SA-coated aluminum dust32. Therefore, as a non-toxic saturated fatty acid with hydrophobic groups, SA is a green compound for constructing hydrophobic functional coatings. A hydrophobic coating on the surface of B powders may effectively enhance the compatibility between B powder and HTPB.
The method for creating a hydrophobic coating is crucial for treating the surfaces of B powders. Various techniques, such as etching, plasma treatment, and stenciling, have produced hydrophobic surfaces in recent years33,34,35. However, these complex methods necessitate a simplified assembly process to construct the surface coating. Thus, solvent evaporation-induced self-assembly represents an efficient strategy for the one-step synthesis of composite solid particles. By preparing the mixture solution, the solute is dissolved in the solvent and assembled on the surface of the solid particle, utilizing the volatility of the solvent when heated. Consequently, composite particles are formed without requiring any additional treatment. For instance, one can enhance combustion performance by using the solvent evaporation method to coat B powders with high-energy oxidants, fluorides, and energetic polymers, increasing their energy output36. Solvent evaporation-induced self-assembly technology is a simple and efficient method for producing composite solid particles in a single step, significantly improving production efficiency.
In this study, a hydrophobic functional coating was prepared on the surface of B particles using the solvent evaporation-induced self-assembly technique with stearic acid, forming SA@B composite particles. The microstructure and morphological characteristics of SA@B composite particles were analyzed. The composite particles’ hydrophobic properties and the SA coating’s influence on the B particles’ combustion performance were investigated. In addition, the mechanical properties of HTPB composite materials incorporating primary B and SA@B composite particles at varying mass loads were investigated.
Experimental
Materials
Boron powders (5 μm, 98% purity), hydroxyl terminated polybutadiene (hydroxyl value 0.47–0.53 mmol/g), stearic acid (95% purity), and toluene diisocyanate (98% purity) were all purchased from Shanghai McLean Biochemical Technology Co., Ltd. Dioctyl sebacate (85% purity), ethanol (99.7% purity), and nCuO powders (50 nm, 99.9% purity) were purchased from Shanghai Aladdin Biochemical Technology Co., Ltd.
Preparation of SA@B composite particles
The preparation process of SA@B composite particles is shown in Fig. 1. 10 g of B particles is added to 300 mL of ethanol solution, sonicated for 30 min, thoroughly stirred for 3 h, filtered, and dried in a vacuum drying oven at 60 °C to obtain the treated B powders. After that, B powders are added to 500 mL of ethanol solution and ultrasonically dispersed for 30 min. Then, 1.5 g of SA is added to the above dispersion solution and thoroughly stirred at 60 °C for 24 h to prepare the precursor solution. The precursor solution was sprayed into the drying chamber at 80 °Cto obtain SA@B composite particles. In addition, 1 g of B powder and 0.15 g of SA were fully mechanically ground through a mortar to prepare SA/B composite particles.
Preparation of B/HTPB composite materials
The measured dioctyl sebacate (plasticizer) and B particles were then added to HTPB (binding agent) and mechanically mixed for 5 min. Subsequently, toluene diisocyanate (curing agent), the curing agent, was added to the B/HTPB blend. The mixture was then homogenized in a cantilever power electric mixer (JB-80SH) at 1500 RPM for 5 min. The resulting mixture was poured into a dumbbell-shaped mold (130 mm × 35 mm × 15 mm) and deoxidized before being cured in a vacuum drying oven at 60 °C to obtain B/HTPB composite materials. At the same time, SA@B/HTPB composite materials are obtained using the same method.
Material characterization and methods
The micromorphology of SA@B composite particles was analyzed by scanning electron microscope (SEM, Zeiss Sigma 300). The distribution and content of surface elements in SA@B composite particles were observed using energy dispersive X-ray spectroscopy (EDS, Oxford Xplore). The chemical bonds of SA@B composite particles in the 400–4000 cm−1 wave number range were analyzed by Fourier transform infrared (FTIR, Thermo Scientific Nicolet iS20). The composition of SA@B composite particles was analyzed by solid state nuclear magnetic analysis (SSNMR Bruker Avance Neo 400WB). The surface structure of SA@B composite particles was evaluated using X-ray photoelectron spectroscopy (XPS, Thermo Scientific K-Alpha). X-ray diffractometer (XRD, Rigaku Miniflex 600) studied the microstructure and phase evolution with a scanning range of 5–90°. In deionized water and diiodomethane media, the static contact angle of SA@B composite particles was measured using a contact angle/surface tension meter (Dataphysics OCA 20).
The particles were tested using differential scanning calorimetry (DSC) and thermogravimetric analysis (TGA) in a static air atmosphere conducted by simultaneous thermal analysis (TG-DSC, Netzsch STA 449 F3). The oxidation process under natural conditions was studied by heating the samples to 1000 °C in air at a 10 K/min heating rate. During thermal decomposition, the gaseous products of SA@B composite particles were analyzed by thermogravimetric infrared-mass spectrometry (TG-FTIR-MS). The combustion heat of particles was measured at 3 MPa by an RF-C7000 oxygen bomb calorimeter. A high-speed camera photographed the flame during the B/nCuO and SA@B/nCuO combustion processes at a recording rate of 5000 frames per second. At the same time, ignition temperatures of B particles and SA@B composite particles were tested in an environment of pure oxygen. To investigate the combustion of B particles and SA@B composite particles in air. Subsequently, the microstructure and XRD analysis of the reaction products were investigated.
In the particle combustion experiment, B particles and SA@B composite particles were ground with nCuO according to the calculated stoichiometric ratio to obtain B/nCuO and SA@B/nCuO mixtures. A high-speed camera photographed the flames during the two combustion processes. Afterward, the combustion products of the two mixtures were collected, and their microstructure and XRD patterns were analyzed.
The microstructure of SA@B/HTPB composite materials was analyzed using SEM to observe the dispersion of B particles in the HTPB matrix. The composite material samples used in the tensile test were prepared at 120 mm × 25 mm × 10 mm. The mechanical properties of B/HTPB and SA@B/HTPB composite materials were evaluated using a tensile testing machine (Model 68TM-30, American Instron Company) at a tensile speed of 100 mm/min. After tensile fracture, samples were collected to analyze the micromorphology of the fracture section.
Results and discussion
Structure and morphology characterization
Figure 2 displays SEM images of B particles and SA@B composite particles corresponding to EDS element mapping. The self-assembly occurred on the surface of B particles when a mixed solution was prepared, and the volatility of the solvent was exploited through heating, resulting in the formation of the SA@B composite particles. Figure 2a shows the irregular microstructure of the amorphous B particles and many aggregation phenomena. However, as shown in Fig. 2b, the particle size of the SA@B composite particles assembled by self-assembly induced by solvent evaporation is significantly smaller than that of particle B, although some agglomeration still exists. This is mainly due to the erosion of the B2O3 shell of ethanol and the spray refinement effect. Figures S1 and S2 show the SEM image of YC@B and SA/B composite particles and the particle size distribution of B, YC@B, SA/B composite particles, and SA@B composite particles, respectively. The particle size of the four kinds of particles is mainly distributed in the range of 1.0–10.0 μm. The average particle sizes of B, YC@B, SA/B composite particles, and SA@B composite particles were 4.9 μm, 4.3 μm, 6.8 μm and 6.3 μm, respectively. The particle size of YC@B decreases slightly, while that of SA/B composite particles and SA@B composite particles increases. The main reason is that the agglomeration phenomenon of B particles after ethanol treatment is reduced. In contrast, the agglomeration phenomenon of SA/B composite particles and SA@B composite particles is increasingly apparent, although the particle size is reduced. Figure 2c shows the EDS mapping images of SA@B composite particles. It can be observed that C and O elements are uniformly distributed on the surface of SA@B composite particles. The presence of C and O elements on the surface of SA@B composite particles is mainly due to SA carbon chains. The results show that the solvent evaporation-induced self-assembly technique successfully applies SA coating to the surface of B particles.
Figure 3 shows the FTIR spectra of the B particle and SA@B composite particle and the XPS spectra of the SA@B composite particle, respectively. Figure 3a displays that for the original B particles, the prominent peaks near 3386 cm-1 and 1393–1562 cm-1 are attributed to the stretching of the O–H and B–O bond on the surface of the original B particles. The prominent peaks occur due to an oxide layer on the B particle surface37. The notable peaks in infrared spectra of SA and SA@B composite particles include the characteristic stretching vibration absorption peak of C=O in SA at 1703 cm-1, as well as the symmetric stretching vibration peak of methylene groups (–CH2) and the asymmetric stretching vibration peak of methyl groups (–CH3) in SA at 2848 cm-1 and 2916 cm-1, respectively38. These peaks correspond to the characteristic peaks of SA, suggesting the presence of SA on the surface of B particles. Figure S3 shows the FTIR spectra of SA/B composite particles. Unlike SA@B composite particles, SA/B composite particles have higher peaks at 3214 cm-1 and 1193–1431 cm-1. They correspond to the O–H and B–O bonds, respectively, indicating that physical mixing does not change the interface properties of B. At the same time, the characteristic peak of SA of SA@B composite particles is higher than that of SA/B composite particles, which also indicates that SA is adsorbed on the surface of B particles under the action of weak interaction force through solvent evaporation. Figure S4 shows the solid-state NMR spectra of SA@B composite particles. The 13C-NMR spectrum mainly comprises 181.6 ppm, 32.8 ppm, 24.7 ppm, and 14.9 ppm peaks. The peak value at chemical shift 181.6 ppm is the carboxyl carbon of the saturated organic chain of SA. The highest peak at 32.8 ppm is the carbon peak of methylene on the stearic acid molecular chain. Most of the 11B-NMR spectrum consists of a peak at 6.3 ppm, mainly the peak of the B atom. Figure 3b–e displays the XPS spectrum of the SA@B composite particles, revealing the characteristic peaks of elements C, B, and O. The XPS spectra of the B particles element reveal that the B peak is 188.3 eV and the B2O3 peak is 189.5 eV. The XPS spectral peak of C element is 284.8 eV, 286.0 eV, and 289.5 eV, corresponding to carbon–carbon (C–C), carbon-hydrogen (C–H), and carbon–oxygen (C–O) bonds of SA respectively. The XPS spectrum of the O element displays two peaks, one at 532.2 eV and the other at 533.4 eV. These peaks are attributed to SA’s C–O bond and COOH components39. Consequently, both FTIR, SSNMR, and XPS results indicate that the surface of B particles is coated with SA, thereby successfully preparing SA@B composite particles.
Dispersion stability and hydrophobicity of SA@B composite particles in water
Figures 4 and S5 illustrate the interface characteristics of the two particles by comparing the states and contact angles of the original B particles and the SA@B composite particles in aqueous conditions. Upon adding the original B particles, they immediately sink to the bottom, where they appear dispersed within the water. The original B particles have a static contact angle of 16.39º in water. The SA/B composite particles behave in the same state as the original B particles in water, settling to the bottom of the water, and the static contact angle of the SA/B composite particles is 23.5º. After adding water to the SA@B composite particles, they are seen suspended on the liquid surface, creating a ‘mirror effect’40. This causes the static contact angle to increase to 136.02º directly. This indicates that a low surface energy SA layer forms on the surface of polar B molecules, transforming the hydrophilic interface of polar B molecules into a hydrophobic interface. To confirm the decrease in the surface free energy (SFE) of B particles after hydrophobic treatment, we estimated the SFE of the original B particles and SA@B composite particles based on the contact angle data of two liquids (water and methylene iodide). Figures 4b and S6 and Table 1 give data on the contact angle and surface free energy of B, SA/B composite particles, and SA@B composite particles in two liquid media. The SFE values are 82.5 mJ/m-2 for the original B particles, 78.3 mJ/m-2 for the SA/B composite particles, and 57.1 mJ/m-2 for the SA@B composite particles. The SFE of the SA@B composite particles decreases, and the static contact angle increases. The surface of the SA@B composite particle enables the formation of a droplet in the ‘Cassie state,’ indicating that the particles’ hydrophobic properties have been successfully achieved41. Figure 4c shows the transformation of hydrophilic B particles to hydrophobic B particles after SA coating. Looking at the macroscopic image of the tablet composed of the original B particles, it is clear that it does not support the presence of liquid water droplets because liquid water droplets penetrate deep inside the tablet. Instead, water droplets can be seen suspended on a laminated sheet composed of SA@B composite particles. Therefore, by constructing SA coating on the surface of B particles, the B particle interface is successfully transformed into a hydrophobic interface.
(a) Contact angle images of water and diiodomethane for B particles and SA@B composite particles. (b) The surface free energy of B particles and SA@B composite particles was calculated from water and diiodomethane (W-D), respectively. (c) The hydrophobic strategy of SA@B composite particles imitating the lotus leaf.
The influence of SA coating on the combustion performance of B particles
To study the effect of SA coating on the oxidation performance of B powders in air, TGA and DSC experiments were conducted on two kinds of samples, and the results are presented in Figs. 5 and S7. The heating rate of both B particles, SA/B composite particles, and SA@B composite particles in an air atmosphere is 10 °C/min, with the temperature increasing from 30 to 1000 °C. The process can be divided into two stages for the TG curve of pure B particles. In the first stage, mass loss occurs in the temperature range of about 75–200 °C, with a weight loss of about 12.94%; in the second stage, mass gain occurs at temperatures of about 500–1000 °C, with weight gain of about 85.16%. In the first stage, the mass loss of the B particles is particularly significant. From the DTG curve of the pure B particles, a sharp peak is observed at approximately 122 °C, associated with the decomposition temperature range of H3BO3. Meanwhile, the mass loss is attributed to the loss of impurities on the surface of the B particles, reaching a weight loss of 12.94%. The natural oxide layer on the surface of pure B particles inhibits their combustion, which may lead to a prolonged ignition delay time and a noticeable sintering phenomenon in the B particles42. The weight loss rate of SA/B composite particles in the first stage is about 24.85%, and the weight gain in the second stage is about 74.80%. It is mainly due to the loss of impurities on the surface of B particles and the thermal decomposition of SA, while the slight decrease in the oxidation weight of B may be due to the competition between SA and the thermal decomposition products of SA and B for oxygen. For the thermogravimetric spectrum of SA@B composite particles, mass loss occurs in the temperature range of 100 °C to 300 °C in the first stage, with a weight loss rate of approximately 12.61%. In the second stage, the mass increase occurs at a temperature range of about 500 °C to 1000 °C, with a weight increase of approximately 119.82%. Unlike pure B particles, SA@B composite particles peaked at 217 °C in the first stage and 776 °C in the second stage. The first stage is mainly the thermal decomposition of SA. The oxidation efficiency of B particles significantly improved, resulting in an 85.16% increase in the weight of the original B particles. The improvement of the oxidation efficiency of B particles may be related to the local dissolution of the primary oxide layer and the synergistic effect of SA42. As can be seen from Figs. 5c and S7 and the data in Table S2, the initial oxidation temperature (Tonset) and maximum exothermic peak (Tmax) of the SA@B composite particles are lower than those of the native B particles and SA/B composite particles. The initial oxidation temperature and maximum heat release peak of the primary B particles are 775 °C and 806 °C, respectively, and the initial oxidation temperature and maximum heat release peak of the SA/B composite particles are 765 °C and 810 °C, respectively. The initial oxidation temperature and maximum exothermic peak of SA@B composite particles are 747.6 °C and 776 °C, respectively. The results indicate that SA@B composite particles exhibit superior oxidation efficiency in air. The DSC curves show that the enthalpies of oxidation release of primary B particles, SA/B composite particles, and SA@B composite particles are 7976 J/g, 8967 J/g, and 14,056 J/g, respectively. This indicates that both SA/B and SA@B composite particles have high enthalpy of oxidation release, and SA improves the oxidation efficiency of B particles to a certain extent. Figures S8-S11 show the thermogravimetric curves of SA@B composite particles, the mass and infrared gas spectrum generated by the thermal decomposition process, and three-dimensional infrared spectrum images. The presence of O–H out-of-plane bending (600–750 cm-1), C–H stretching (2800–3000 cm-1), and C=C stretching (1620–1680 cm-1) in mass spectrometry and infrared spectral images indicates the possible presence of combustible gases such as methane and acetylene. The mass spectrometry image can detect the apparent peak value when the molecular weight is 18, 28, and 44, which may correspond to H2O, C2H4, or CO and CO2, respectively. Smaller peaks can be detected at molecular weight 2, 16, 26, possibly corresponding to H2, CH4, and C2H2. This indicates that dissociating carbon–carbon (C–C) bonds during SA’s thermal decomposition may produce methane, acetylene, and other flammable gases. This is similar to what Cao et al. reported39. Therefore, the increase in the initial oxidation temperature and enthalpy of the SA@B composite particles may be due to the exothermic heat released from the combustible gas generated by the thermal decomposition of SA.
TG/DTG curves of (a) B particles and (b) SA@B composite particles, respectively, at a heating rate of 10 °C/min in an air atmosphere. (c) The DSC curves of B particles and SA@B composite particles, respectively. (d) The heat of combustion of B particles, SA@B composite particles, and SA/B particles in oxygen atmosphere.
Figure 5d displays the measured calorific value of combustion heat. It can be observed that the combustion heat of SA/B composite particles and SA@B composite particles reaches 21.37 MJ/kg and 30.29 MJ/kg, respectively, which are significantly higher than that of the original B particles. The calorific value of combustion is about 30% and 50% higher than that of original B, respectively. Figure S13 illustrates the XRD curves of the products resulting from the combustion heat tests of B particles, SA/B composite particles, and SA@B composite particles. The combustion products of all three samples detected high-intensity crystallization peaks of boric acid (H3BO3). In the XRD images of the combustion products from the three particles, the relative intensity of the H3BO3 peak for SA@B composite particles is significantly higher than that of B particles and SA/B composite particles. Since SA burns in oxygen to form water and carbon dioxide, H3BO3 may be produced by reacting with water and boron trioxide (B2O3)43. In addition, peaks corresponding to the oxidation product B6O were also detected. Therefore, the SA@B composite particles prepared by the solvent evaporation-induced self-assembly have a higher calorific value of combustion, which can be attributed to the contributions of SA and the dispersion enhancement of B particles44.
Figure S14 illustrates the combustion phenomenon of B particles, SA/B composite particles, and SA@B composite particles in an oxygen atmosphere at 800 °C. Under the oxygen atmosphere, the ignition temperature of B particles, SA/B composite particles, and SA@B composite particles is 760 °C, 755 °C, and 737 °C, respectively. The results show that SA coating reduces the ignition temperature of B particles. Figure S15 shows the images of B particles, SA/B composite particles, and SA@B composite particles in an oxygen atmosphere at 700 °C. There is no obvious ignition of B particles in an oxygen atmosphere at 700 °C. The ignition delay time for SA@B composite particles is 36 s. At T = 36 s, an explosion sound is heard, resulting from the pyrolysis and gasification of SA particles in high-temperature oxygenation. The mixture of SA particles and oxygen has reached its explosion limit. Then, at T = 40 s, an apparent burning phenomenon occurred, and the B particles began to burn. The ignition delay time of SA/B composite particles is 32 s, and the combustion phenomenon of SA/B composite particles is similar to that of SA@B composite particles.
The combustion phenomenon of the original B particles, SA/B composite particles, and SA@B composite particles in the air has been investigated. Figure S16 shows the micromorphology of the reaction products at 700 °C in air. Unlike the atmosphere containing oxygen, in the ambient air atmosphere, there is no observable chemical reaction phenomenon during the entire process of the primary B particles. One can observe that the particle size of the reaction products of SA/B composite particles and SA@B composite particles is significantly larger than that of the original B particles, indicating that the reaction products of the SA@B particles form a large volume aggregate. Figure S17 shows the XRD pattern of the high-temperature reaction products. The XRD curves show crystallization peaks corresponding to B, B2O3, and B6O in the products of the three samples. The peak value of B in the SA@B composite particle products is slightly weak, while the peaks of B2O3 and B6O are relatively high compared with other significant samples45.
Combustion performance of B/nCuO and SA@B/nCuO
To study the combustion process in the atmospheric environment of the original B, SA/B composite particles, and SA@B composite particles, we prepared B/nCuO, SA/B/nCuO, and SA@B/nCuO by mechanically mixing them with nCuO. Figures 6 and S18 display the flame images of the combustion process of B/nCuO, SA/B/nCuO, and SA@B/nCuO. The entire combustion process can be divided into three stages: the pre-combustion stage, the stable combustion stage, and the extinction stage. For B/nCuO samples, during the pre-combustion stage, external energy initially stimulates the sample to ignite B/nCuO locally. Between t = 12 ms and t = 16 ms, B/nCuO burns violently, with the bright flame gradually spreading and ejecting many molten metal particles. The flame expands to a maximum near t = 48 ms, enters a stable combustion phase, and progressively shrinks until extinguished. Throughout the combustion process of the B/nCuO samples, a substantial number of molten solid particles are distinctly dispersed around the flame. On the other hand, considering the overall combustion time, the combustion process is complete from t = 0 ms to t = 108 ms. The green particles observed are likely to be B particles, and the overall flame is in a disordered state. For the SA@B/nCuO sample, in the pre-combustion stage, SA first occurs in a combustion reaction and releases heat. Therefore, when t = 20 ms, the outer flame appears green, the inner flame appears yellow, and the flame gradually spreads steadily. Near t = 80 ms, the flame expands to its limit an slowly burns until it is extinguished. The entire combustion process of SA@B/nCuO samples, compared to the B/nCuO samples, demonstrates no significant diffusion of solid particles around the flame. The green flame signature of B particles can be observed throughout the combustion process. From the overall combustion time perspective, the combustion process of SA@B/nCuO finishes roughly from t = 0 ms to t = 180 ms, which is longer than the stable combustion time of the original B/nCuO. The SA/B/nCuO sample’s combustion process is similar to that of the SA@B/nCuO sample, except that the SA@B/nCuO sample’s combustion flame intensity is weaker than that of the B/nCuO sample and the SA@B/nCuO sample. However, fewer molten metal particles exist than in the B/nCuO samples, reducing the two-phase flow loss. The results indicate that SA can enhance B particles’ stability and combustion performance during combustion43.
Figure 7 shows the combustion emission spectra curves of B/nCuO, SA@B/nCuO and SA/B/nCuO. The emission spectra of the three samples show the same characteristic emission peaks at 686 nm and 826 nm. The emission spectrum of the SA@B/nCuO complex exhibits a stronger characteristic emission peak at 588 nm. The strong characteristic peaks at 686 nm to 826 nm can be attributed to BO246. The strong characteristic peak observed at 588 nm in the SA@B/nCuO sample is likely associated with the C2 free radical47. This peak corresponds to a small-molecule intermediate product formed during the thermal decomposition process mediated by SA. The spectral intensity of SA@B/nCuO is stronger than that of B/nCuO. The presence of SA has been shown to improve the combustion efficiency of B powders during the combustion process of SA@B/nCuO.
Figure 8a–c shows the SEM images of the combustion products for B/nCuO, SA/B/nCuO, and SA@B/nCuO. In the combustion products of B/nCuO, numerous larger solid particles are present. This is mainly because the fine molten metal particles diffuse and come into contact with each other, forming larger solid particles. The particle size of the combustion products for SA/B/nCuO and SA@B/nCuO is significantly smaller than that of B/nCuO. Due to the presence of SA, the SA@B composite particles exhibit good dispersion. Therefore, B melts and agglomerates during combustion, forming small, rough-surfaced solid particles. The results indicate that SA coating effectively enhances the dispersal of B particles and mitigates the accumulation of combustion products48.
Figure 8d shows the XRD curves of the combustion products of B/nCuO, SA/B/nCuO, and SA@B/nCuO. The stronger peaks in the XRD images are related to the crystallization peaks of copper. This is the result of nCuO participating in a thermite reaction. The crystallization peaks of cuprous oxide (Cu2O) and incomplete nCuO were also observed. The intensity of the peaks corresponding to Cu and Cu2O in the combustion products of SA@B/nCuO is significantly higher than that in the B/nCuO. Figures S19–S21 shows the XPS curves of B/nCuO, SA/B/CuO, and SA@B/nCuO combustion products. In addition to the peak value of Cu in the combustion products of the three samples, the peak value of B2O3 was also detected in the B1S acceptable spectrum. No peak of B particles was observed, indicating that B has fully participated in the combustion reaction. The results show that the presence of the SA coating can improve the dispersion of B, increase the contact area with nCuO, and improve the combustion performance of B particles49.
The influence of SA coating on the mechanical properties of composite materials
To investigate the impact of hydrophobic SA coating on the mechanical properties of SA@B/HTPB composite materials, we prepared composite materials containing B particles and SA@B composite particles at mass loads of 20%, 35%, and 50%. However, due to impurities on the surface of B particles, the slurry prepared from 50% B particles has a high viscosity, making it unsuitable for preparing HTPB matrix composite materials. By comparing the preparation Videos S1 and S2 of B particles and SA@B composite particles mixed with HTPB respectively under the same mass load, it can be observed that the HTPB slurry composed of SA@B composite particles exhibits good fluidity. The results showed that the presence of SA coating effectively prevented the reaction of H3BO3, B2O3, and HTPB and reduced the viscosity of the paste. The dispersion state of B particles in HTPB matrix composite materials significantly affects their macroscopic mechanical properties. To analyze the dispersion of particles in the HTPB matrix, we collected SEM images of cross-sections of B/HTPB and SA@B/HTPB composites. Figure 9a–b shows the aggregation of large B particles. The B particles are irregularly dispersed within the HTPB matrix, and their distribution is relatively poor. As the mass load of B particles increases, the degree of agglomeration becomes more severe, leading to deteriorating dispersion. As shown in Fig. 9c–e, under the same mass load, the B particles in the SA@B/HTPB composite materials display less aggregation than those in the B/HTPB composite materials, and the particles exhibit improved dispersion within the HTPB matrix. By comparing the cross-sectional morphologies of B/HTPB composite materials under the same mass load and different magnifications, it is observed that the surface of the B/HTPB matrix appears rough. In contrast, the matrix in the SA@B/HTPB composite materials is noticeably flatter. This indicates that SA coating can effectively enhance the dispersal of B in HTPB and improve the compatibility between B and HTPB50.
SEM images of the cross-sectional views for HTPB matrix composite materials are presented, showing (a) B particles at a 20% mass loading, (b) B particles at a 35% mass loading, (c) SA@B composite particles at a 20% mass loading, (d) SA@B composite particles at a 35% mass loading, and (e) SA@B composite particles at a 50% mass loading.
Figure 10 and Table S1, respectively, show stress–strain curves of B/HTPB and SA@B/HTPB composite materials under different mass loads and summarize the mechanical differences of B/HTPB and SA@B/HTPB composite materials and the mechanical properties parameters obtained from the stress–strain curves. The experimental results indicate that the tensile strength of the SA@B/HTPB composite materials exceeds that of the B/HTPB composite materials. This enhancement is attributed to the SA coating on the B particles’ surface, which enhances the tensile strength by significantly improving the dispersion of the B particles within the composite material. Due to a hydrophobic structure on the surface of B particles, the agglomeration state between each boron particle is weakened, and the weakening problem of the ‘reinforcing effect’ caused by local defects is avoided51. At the same time, SA@B/HTPB composite materials with a mass fraction of SA@B composite particles up to 50% can be prepared, and the tensile strength of 50% SA@B/HTPB composite materials is significantly higher than that of other composite materials. The high-quality load exerted by the SA@B composite particles enhances the ‘reinforcing effect’ of the SA@B/HTPB composite materials. Young’s modulus of SA@B/HTPB composite materials also increases with the mass loading of SA@B composite particles. The results indicate that the hardening effect of high mass loading on SA@B/HTPB composite materials is significant. Therefore, constructing a surface coating of B particles can improve the mechanical properties of SA@B/HTPB composite materials to a certain extent.
Boron-based rich fuel solid rocket propellant is a kind of particle-filled composite material, and its mechanical properties are related to the properties of the particles, the matrix, and the particle/matrix interface. The damage modes include brittle fracture of solid particles, tearing of the matrix, and interfacial adhesion between the matrix and solid particles. However, in complex real-world environments, the damage mode often results from the coupled effects of various damage mechanisms. Under this coupled effect, the stress transfer throughout the system is weakened, diminishing the reinforcing impact of the solid packing. To observe the morphology of the interface structure in the two composite materials, SEM images were captured of the fracture surfaces of the samples, and the findings are presented in Fig. 11, respectively52.
SEM images of the tensile fracture surfaces for HTPB matrix composite materials are presented, illustrating the distribution of (a) B particles at a 20% mass loading, (b) B particles at a 35% mass loading, (c) SA@B composite particles at a 20% mass loading, (d) SA@B composite particles at a 35% mass loading, and (e) SA@B composite particles at a 50% mass loading.
Figure 11a–b shows bare solid particles and pits left after the solid particles fell off, and prominent platforms are observed. Additionally, transparent B particles are visible upon examining the enlarged image. The results show that the damage modes of B/HTPB composite materials during the tensile process are primarily dehumidifying solid particles, brittle fracture of solid particles, and tearing of the matrix. In Fig. 11c–e, compared to B/HTPB composite materials, SA@B/HTPB composite materials exhibit fewer pits. The matrix in these figures appears bumpy, with more adhesive matrix wrapping around the solid particles. Additionally, the SA@B/HTPB composite materials exhibit a prominent platform in the enlarged image, which suggests that matrix tearing occurred during the stretching process53. Therefore, the primary damage mode in SA@B/HTPB composite materials is caused by damage to the adhesive matrix. This is mainly due to the synergistic effect of good dispersion of B particles and strong interface interaction, which enhances the stress transfer of SA@B/HTPB composite materials during the tensile process. On the other hand, the hydrophobic end of the SA molecule on the surface of the B particle is adsorbed onto the surface of the HTPB polymer. This adsorption forms a robust interfacial interaction, which limits the migration of HTPB polymer chains and reduces the effect of stress concentration. As a result, effective load transfer is realized. The tensile fracture morphology of B/HTPB composite materials and SA@B/HTPB composite materials proves this.
Figure 12a–b and Table S2 compare the combustion properties, mechanical properties, and HTPB composites of SA@B and SA@B/HTPB composites with those of representative literature. SA@B composite particles exhibit the high calorific value of combustion and excellent thermal properties9,26,54 The calorific value of combustion is higher than most published data for modified boron particles, about 50% higher. SA@B/HTPB composites exhibit higher maximum tensile strength and Young’s modulus, about 16% higher than those reported for boron-based HTPB composites8,50,55. The improvement of the combustion performance of B particles is mainly attributed to the contribution of SA. In the thermite of SA@B/CuO, SA first burns to release heat, and a large amount of heat promotes the oxidation process of B, as described in sections “The influence of SA coating on the combustion performance of B particles” and “Combustion performance of B/nCuO and SA@B/nCuO”. Thus, SA@B exhibits a low ignition temperature, a high heat of combustion, and fewer combustion products. The improvement of B particle interface characteristics mainly improves the compatibility with HTPB and then affects the preparation process and mechanical properties of B/HTPB. Thus, B/HTPB solid fuels with high energy density and excellent mechanical properties are possible.
Conclusion
In this study, a hydrophobic coating was successfully applied to the surface of B particles using solvent evaporation-induced self-assembly technology. SA@B composite particles exhibit remarkable hydrophobicity. SA@B The oxidation gain of the composite particle is 119.82%, and the calorific value of combustion is 30.29 MJ/kg, which is about 50% higher than that of the original B particle. The combustion test results also show that the duration of the combustion process for SA@B/CuO is noticeably longer, the molten solid particles do not spread obviously, and the flame’s process stability is maintained. In addition, the SA coating significantly improves the dispersibility of B particles in HTPB and enhances its compatibility with HTPB. SA@B/HTPB composite materials with a mass loading of 50% were successfully prepared, and SA@B/HTPB composite materials exhibit a tensile strength significantly higher than that of B/HTPB composite materials. The tensile strength of 50% SA@B/HTPB composite materials reaches 2.46 MPa, and Young’s modulus peaks at 7.48 MPa. According to the analysis of the tensile fracture morphology of the two composite materials, the primary mode of damage in the SA@B/HTPB composite materials is damage to the binder matrix. Due to the excellent dispersion of B particles within the HTPB matrix and the strong interfacial bonding between HTPB and the matrix, effective stress transfer occurs during the tensile process. Therefore, the hydrophobic coating constructed on the surface of B particles effectively promotes energy release efficiency and improves the mechanical properties of HTPB matrix composite materials. This strategy is expected to be applied to boron-based fuel rich solid rocket propellant.
Data availability
All data generated or analysed during this study are included in this published article [and its supplementary information files].
References
Beckstead, M. W., Puduppakkam, K., Thakre, P. & Yang, V. Modeling of combustion and ignition of solid-propellant ingredients. Prog. Energy Combust. Sci. 33(6), 497–551 (2007).
Pang, W. Q. et al. Boron-based composite energetic materials (B-CEMs): Preparation, combustion and applications. Progress Energy Combust. Sci. https://doi.org/10.1016/j.pecs.2022.101038 (2022).
Trache, D., Klapoetke, T. M., Maiz, L., Abd-Elghany, M. & DeLuca, L. T. Recent advances in new oxidizers for solid rocket propulsion. Green Chem. 19(20), 4711–4736 (2017).
Yang, D., Liu, R., Li, W., & Yan Q.L. Recent advances on the preparation and combustion performances of boron-based alloy fuels. Fuel (2023).
Kumar, P., Varshney, M. & Manash, A. Combustion performance studies of aluminum and boron based composite solid propellants in sub-atmospheric pressure regimes. Propuls. Power Res. 8(4), 329–338 (2019).
Pal, Y., Mahottamananda, S. N., Palateerdham, S. K., Ingenito, A. & Trache, D. Oxidation reaction kinetics of HTPB-boron carbide/polytetrafluoroethylene formulations as a solid fuel. Fuel 352, 129042 (2023).
Tian, H. et al. Effect of metal and metalloid solid-fuel additives on performance and nozzle ablation in a hydroxy-terminated polybutadiene based hybrid rocket motor. Aerospace Sci. Technol. 123, 107493 (2022).
Jiang, Y. et al. Enhancing mechanical and combustion performance of boron/polymer composites via boron particle functionalization. ACS Appl. Mater. Interfaces. 13(24), 28908–28915 (2021).
Xiao, F., Chen, C., Chen, Z. & Hu, J. In situ precise construction of surface-activated boron powders: A new strategy to synergistically improve the interface properties and enhance combustion performance of boron. Fuel 351, 128995 (2023).
Yang, D. et al. Synthesis of metallized kerosene gel and its characterization for propulsion applications. Fuel 262, 116684 (2020).
Han, L. et al. Preparation and combustion mechanism of boron-based high-energy fuels. Catalysts 13(2), 378 (2023).
Liu, Y. et al. High calorific values boron powder: Ignition and combustion mechanism, surface modification strategies and properties. Molecules 28(7), 3209 (2023).
Yuan, J. et al. Combustion and agglomeration characteristics of boron particles in boron-containing fuel-rich propellant. Combust. Flame 232, 111551 (2021).
Suryanarayana, C. & Al-Aqeeli, N. Mechanically alloyed nanocomposites. Prog. Mater Sci. 58(4), 383–502 (2013).
Sun, Y., Ren, H., Jiao, Q., Schoenitz, M. & Dreizin, E. L. Oxidation, ignition and combustion behaviors of differently prepared boron-magnesium composites. Combust. Flame 221, 11–19 (2020).
Antonov, I. et al. Discovery of discrete stages in the oxidation of exo-tetrahydrodicyclopentadiene (C<sub>10</sub>H<sub>16</sub>) droplets doped with titanium-aluminum-boron reactive mixed-metal nanopowder. J. Phys. Chem. Lett. 13(41), 9777–9785 (2022).
Debnath, A., Pal, Y., Mahottamananda, S. N. & Trache, D. Unraveling the role of dual Ti/Mg metals on the ignition and combustion behavior of HTPB-boron-based fuel. Defence Technol. 32, 134–143 (2024).
Yang, T. et al. Combustion performance of aluminum modified boron nanoparticles coated with silane coupling agent. Combust. Flame 264, 113442 (2024).
Huang, S., Deng, S., Jiang, Y. & Zheng, X. Experimental effective metal oxides to enhance boron combustion. Combust. Flame 205, 278–285 (2019).
Agarwal, P. P. K., Jensen, D., Chen, C.-H., Rioux, R. M. & Matsoukas, T. Surface-functionalized boron nanoparticles with reduced oxide content by nonthermal plasma processing for nanoenergetic applications. ACS Appl. Mater. Interfaces. 13(5), 6844–6853 (2021).
Lebedeva, E. A., Astaf’eva, S. A., Istomina, T. S. & Badica, P. Combustion products agglomeration of propellant containing boron with fluorinated coatings. Combust. Flame 238, 111749 (2022).
Valluri, S. K., Schoenitz, M. & Dreizin, E. Bismuth fluoride-coated boron powders as enhanced fuels. Combust. Flame 221, 1–10 (2020).
Hedman, T. D., Demko, A. R. & Kalman, J. Enhanced ignition of milled boron-polytetrafluoroethylene mixtures. Combust. Flame 198, 112–119 (2018).
Valluri, S. K., Ravi, K. K., Schoenitz, M. & Dreizin, E. L. Effect of boron content in B·BiF<sub>3</sub> and B·Bi composites on their ignition and combustion. Combust. Flame 215, 78–85 (2020).
Wang, J. et al. Surface engineering boron/graphite fluoride composite with enhanced ignition and combustion performances. Fuel 323, 124374 (2022).
Baek, J. et al. Effect of fluoroalkylsilane surface functionalization on boron combustion. ACS Appl. Mater. Interfaces. 14(17), 20190–20196 (2022).
Yan, L., Zhu, B., Chen, J. & Sun, Y. Study on nano-boron particles modified by PVDF to enhance the combustion characteristics. Combust. Flame 248, 112556 (2023).
Liu, J., Wang, D., Xu, G. & Li, F. Point-to-point efficient grafting improved compatibility of boron-based fuel-rich propellants. ACS Omega 8(40), 37309–37316 (2023).
Liu, Y.-F., Chen, Y., Shi, L. & Yao, W. S. Preparation of B<SUP>AP</SUP> composite particles and their effects on rheological properties of HTPB/B/AP Slurries. J. Energ. Mater. 32(2), 71–79 (2014).
Prudnikov, E. et al. Self-assembled fatty acid crystalline coatings display superhydrophobic antimicrobial properties. Mater. Today Bio 18, 100516 (2023).
Guo, X., Man, S., Li, Y. & Liang, T. A novel fluorine-free design of superhydrophobic nano-Al/NiO (II) energetic film with promising exothermic performance. Mater. Lett. 347, 134438 (2023).
Li, N. et al. Effect of stearic acid coating on the explosion characteristics of aluminum dust. Fuel 320, 123880 (2022).
Chen, C. et al. Study on exothermic effect of surface modified porous aluminum. Colloids Surf. a-Physicochem. Eng. Aspects 671, 131649 (2023).
Darmanin, T. & Guittard, F. Recent advances in the potential applications of bioinspired superhydrophobic materials. J. Mater. Chem. A 2(39), 16319–16359 (2014).
Dimitrakellis, P. & Gogolides, E. Hydrophobic and superhydrophobic surfaces fabricated using atmospheric pressure cold plasma technology: A review. Adv. Coll. Interface. Sci. 254, 1–21 (2018).
Liu, R., Yang, D., Xiong, K., Wang, Y. L. & Yan, Q.-L. Fabrication and characterization of multi-scale coated boron powders with improved combustion performance: A brief review. Defence Technol. 31, 27–40 (2024).
Chintersingh, K.-L., Schoenitz, M. & Dreizin, E. L. Oxidation kinetics and combustion of boron particles with modified surface. Combust. Flame 173, 288–295 (2016).
Han, L. et al. Lotus effect inspired hydrophobic strategy for stable Zn metal anodes. Adv. Mater. https://doi.org/10.1002/adma.202308086 (2023).
Zhang, Y. et al. Reaction mechanism of stearic acid pyrolysis via reactive molecular dynamics simulation and TG-IR technology. Renew. Energy 217, 119115 (2023).
Yao, N. et al. Stearic acid coating on circulating fluidized bed combustion fly ashes and its effect on the mechanical performance of polymer composites. Appl. Surf. Sci. 279, 109–115 (2013).
Xiong, Z. et al. Surface hydrophobic modification of starch with bio-based epoxy resins to fabricate high-performance polylactide composite materials. Compos. Sci. Technol. 94, 16–22 (2014).
Ojha, P. K. & Karmakar, S. Boron for liquid fuel engines: A review on synthesis, dispersion stability in liquid fuel, and combustion aspects. Prog. Aerosp. Sci. 100, 18–45 (2018).
Li, W. et al. Thermal decomposition, flame propagation, and combustion reactions behaviours of stearic acid by experiments and molecular dynamic simulation. Chem. Eng. J. 461, 141906 (2023).
Padwal, M. B., Castaneda, D. A. & Natan, B. Hypergolic combustion of boron based propellants. Proc. Combust. Inst. 38(4), 6703–6711 (2021).
Keerthi, V., Nie, H., Pisharath, S. & Hng, H. H. Combustion characteristics of fluoropolymer coated boron powders. Combust. Sci. Technol. 194(6), 1183–1198 (2022).
Huang, X. et al. Comparison on ignition and combustion of AlMgB composite fuel and B fuel. Chem. Eng. J. 450, 138133 (2022).
Do, H. & Carter, C. Hydrocarbon fuel concentration measurement in reacting flows using short-gated emission spectra of laser induced plasma. Combust. Flame 160(3), 601–609 (2013).
Wang, S. J. et al. Enhanced combustion behavior of TKX-50/B/NC composites via electrospray. J. Energet. Mater. https://doi.org/10.2139/ssrn.4101144 (2022).
Wang, J. et al. Ignition and combustion characteristics of B/NC/CuO thermite microparticles. Metals 12(9), 1419 (2022).
Jiang, Y. et al. Tailoring the mechanical and combustion performance of B/HTPB composite solid fuel with covalent interfaces. Compos. Sci. Technol. 245, 110350 (2024).
Nie, K. B., Wang, X. J., Deng, K. K., Hu, X. S. & Wu, K. Magnesium matrix composite reinforced by nanoparticles: A review. J. Magnesium Alloys 9(1), 57–77 (2021).
Lv, X. et al. The effect of Al/oxidizers interfacial structure on the mechanical properties of composite propellants. Polymer Test. 126, 108167 (2023).
Chen, X. et al. Compressive mechanical properties of HTPB propellant at low temperatures and high strain rates. Res. Phys. 7, 4079–4084 (2017).
Hu, Y. et al. Encapsulated boron-based energetic spherical composites with improved reaction efficiency and combustion performance. Chem. Eng. J. 433, 134478 (2022).
Dongwon, K. et al. Mechanical and combustion properties of fluoroalkylsilane surface-functionalized boron/HTPB composite. Combust. Flame https://doi.org/10.1016/j.combustflame.2024.113621 (2024).
Acknowledgements
This work was supported by Natural Science Foundation of Shanxi Province (No.202203021221120) and the 19th graduate science and technology project of North University of China (No.20231966).
Author information
Authors and Affiliations
Contributions
Jiaxin Lu: Conceptualization, Methodology, Investigation, Writing—original draft. Chong Chen: Data curation. Bobo Zhang: Resources. Kang Niu: Formal analysis. Fei Xiao: Project administration, Writing—review & editing. Taixin Liang: Supervision. All authors reviewed the manuscript.
Corresponding authors
Ethics declarations
Competing interests
The authors declare no competing interests.
Additional information
Publisher's note
Springer Nature remains neutral with regard to jurisdictional claims in published maps and institutional affiliations.
Supplementary Information
Rights and permissions
Open Access This article is licensed under a Creative Commons Attribution-NonCommercial-NoDerivatives 4.0 International License, which permits any non-commercial use, sharing, distribution and reproduction in any medium or format, as long as you give appropriate credit to the original author(s) and the source, provide a link to the Creative Commons licence, and indicate if you modified the licensed material. You do not have permission under this licence to share adapted material derived from this article or parts of it. The images or other third party material in this article are included in the article’s Creative Commons licence, unless indicated otherwise in a credit line to the material. If material is not included in the article’s Creative Commons licence and your intended use is not permitted by statutory regulation or exceeds the permitted use, you will need to obtain permission directly from the copyright holder. To view a copy of this licence, visit http://creativecommons.org/licenses/by-nc-nd/4.0/.
About this article
Cite this article
Lu, J., Chen, C., Zhang, B. et al. Combustion and mechanical properties enhancement strategy based on stearic acid surface activated boron powders. Sci Rep 14, 21979 (2024). https://doi.org/10.1038/s41598-024-71246-0
Received:
Accepted:
Published:
DOI: https://doi.org/10.1038/s41598-024-71246-0
Keywords
This article is cited by
-
Thermal Decomposition and Combustion Performance of Energetic Materials/Ti Systems
Korean Journal of Chemical Engineering (2025)